Services
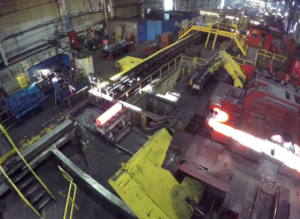
State-Of-The-Art Facilities and Complete Capabilities
Standard Forged Products is one of the most advanced manufacturers in the world. Each of our manufacturing plants comes equipped with the latest Programmable Logic Controllers technology that provide quicker changeover and closer tolerances. Our forging and machining capabilities along with our people are our strongest assets.
Whether you need your axles rough forged or rough machined, finished or in mounted sets, Standard Forged Products, LLC can meet all your axle needs.
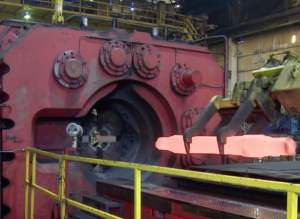
Forging
After the raw material is heated to 2,200˚F, it is automatically transferred to our state of the art GFM (General Forging Machine). An electronic program controls the process so that each piece of raw material is forged into its’ desired state in the most efficient manner. After exiting the forging machine the newly forged axle then gets torched on both ends, stamped, and migrated to our automated heat treat line and furnaces. After completion of heat treating the axles are stored in heat lots and tested to meet all applicable AAR requirements before being released for machining.
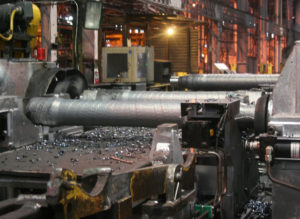
Rough Turning
The axle is milled to length and a journal collar and center hole are applied. An ultrasonic inspection is conducted to insure internal axle quality. The axle is stamped with ID numbers and is sent to one of three separate rough turn lines. After rough turning, all axles are 100% dimensionally inspected.